S2K Commerce - Shopping Cart
S2K Commerce - Products Dropdown
S2K Commerce - Order Entry
Expanded Technologies
Wrap Around Floor Savers, 3/4" x 3-1/8", Gray, 1000 Pack
Item #:
WRAPGY.75-1K
1000/Pk
675.73
PK
Quantity:
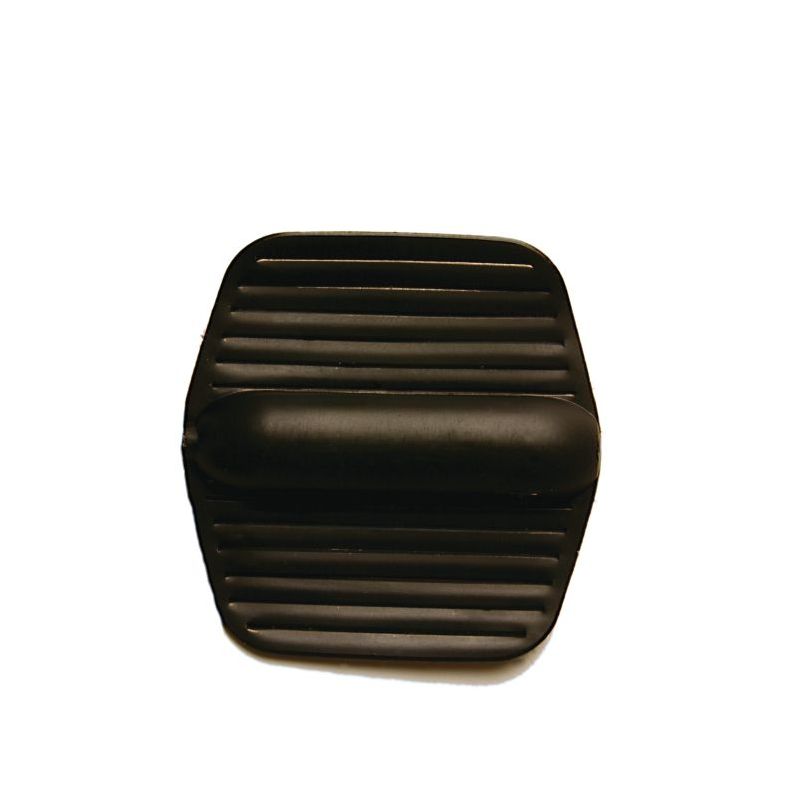
- Wrap-Around® Floor Savers® provide floor protection for chairs with sled bases.
- Easy to apply, they attach to themselves for a longer lasting, improved hold, and conform to glides or rails to achieve a perfect fit.
- These floor protectors prevent damage to all types of hard flooring and are available in grey, black, and clear.
- Recommended for preventing floor damage on hardwood floors, VCT, vinyl, linoleum, and finished concrete and ceramic tile floors.
Floor Protection
Brand
Expanded Technologies
Subcategory
Floor Protection
Collection
Floor Savers
Color
Gray
Size
3/4" x 3-1/8"
Type
Wrap Around
Per/Pk
1000 / PK